First of all, let me give you a quick summary of the cycle view of the supply chain.
There are two different ways to view the processes performed in a supply chain:
1) Cycle view,
2) Push/pull view.
Cycle view
The processes in a supply chain are divided into a series of cycles, each performed at the interface between two successive stages of a supply chain.
All supply chain processes can be broken down into the following four process cycles:
- Customer order cycle
- Replenishment cycle
- Manufacturing cycle
- Procurement cycle
Each cycle occurs at the interface between two successive stages of the supply chain. Not every supply chain will have all four cycles separated. For example, a grocery supply chain in which a retailer stock finished goods inventories and places replenishment orders, which a distributor is likely to have all four cycles separated.
Dell, in contrast, sells directly to customers, thus bypassing the retailer and distributor.
A cycle view of a supply chain is very useful when considering operational decisions because it clearly specifies the rules and responsibilities of each member of the supply chain. The detailed process description of a supply chain in the cycle view forces a supply chain designer to consider the infrastructure required to support these processes.
The cycle view of a supply chain is useful, for example, when setting up information systems to support supply chain operations, as process ownership and objectives are clearly defined.
Customer order cycle
The customer order cycle occurs at the customer/retailer interface and includes all processes directly involved in receiving and filling the customer’s order.
Typically, the customer initiates this cycle at a retailer site and the cycle primarily involves filling customer demand. The retailer’s interaction with the customer starts when the customer arrives or contact is initiated and ends when the customer receives the order.
The processes involved in the customer order cycle include:
- Customer arrival
- Customer order entry
- Customer order fulfillment
- Customer order receiving
Customer arrival
- The customer walks into a supermarket to make a purchase
- The customer calls a mail order telemarketing center
- The customer uses the web or an electronic link to a mail order form
From the supply chain perspective, the key flow in this process is the customer’s arrival. The goal is to facilitate the contact between the customer and the appropriate product so that the customer’s arrival turns into a customer order.
At a supermarket, facilitating a customer order may involve managing customer flows and product displays. At a telemarketing center, it may mean ensuring that the customer does not have to wait on hold for too long.
It may also mean having systems in place so that sales representatives can answer customer queries in a way that turns calls into orders. At a website, a key system may be searched capabilities with tools. That allow customers to quickly locate and view products that interest them.
The objective of the customer arrival process is to maximize the conversion of customer arrivals to customer orders.
Customer order entry
The term “customer order entry” refers to customers informing the retailer what products they want to purchase and the retailer allocating products to customers. At a supermarket, order entry may take the form of customers loading all items that they intend to purchase onto their carts.
At a mail-order firm’s telemarketing center or website, order entry involves customers informing the retailer of the items and quantities they selected.
The objective of the customer order entry process is to ensure that the order entry is quick, accurate, and communicated to all other supply chain processes that are affected by it.
Customer order fulfillment
During this process, the customer’s order is filled and sent to the customer. At a supermarket, the customer performs this process. At a mail order firm this process includes picking the order from inventory, packaging it, and shipping it to the customer.
The objective of the customer order fulfillment process is to get the correct orders to customers by the promised due dates at the lowest possible cost.
Customer order receiving
During this process, the customer receives the order and takes ownership. Records of this receipt are updated and payment completed. At a supermarket, receiving occurs at the checkout counter. For a mail order firm, receiving occurs when the product is delivered to the customer.
Replenishment cycle
The replenishment cycle occurs at the retailer/distributor interface and includes all processes involved in replenishing retailer inventory. It is initiated when a retailer places an order to replenish inventories to meet future demand.
A replenishment cycle may be triggered at a supermarket that is running out of stock of detergent or at a mail order firm that is low in stock of a particular shirt.
The replenishment cycle is similar to the customer order cycle except that the retailer is now the customer. The objective of the replenishment cycle is to replenish inventories at the retailer at minimum cost while providing high product availability.
The processes involved in the replenishment cycle include:
- Retail order trigger
- Retail order entry
- Retail order fulfillment
- Retail order receiving
Retail order trigger
The objective when setting replenishment order triggers is to maximize profitability by ensuring economies of scale and balancing product availability and the cost of holding inventory. The outcome of the retail order trigger process is the generation of a replenishment order that is ready to be passed on to the distributor or manufacturer.
Retail order entry
This process is similar to customer order entry at the retailer. The only difference is that the retailer is now the customer placing the order that is conveyed to the distributor. This may be done electronically or by some other medium. Inventory or production is then allocated to the retail order.
The objective of the retail order entry process is that an order is entered accurately and conveyed quickly to all supply chain processes affected by the order.
Retail order fulfillment
This process is very similar to customer order fulfillment except that it takes place at the distributor. A key difference is the size of each order as customer orders tend to be much smaller than replenishment orders.
The objectives of the retail order fulfillment are to get the replenishment order to the retailer on time while minimizing costs.
Retail order receiving
Once the replenishment order arrives at a retailer, the retailer must receive it physically and update all inventory records. This process involves product flow from the distributor to the retailer as well as information updates at the retailer and the flow of funds from the retailer to the distributor.
The objective of the retail order receiving process is to update inventories and displays quickly and accurately at the lowest possible cost.
Manufacturing cycle
The manufacturing cycle typically occurs at the distributor/manufacturer (or retailer/manufacturer) interface. This includes all processes involved in replenishing distributor (or retailer) inventory.
The manufacturing cycle view of supply chain is triggered by customer orders (as is the case with Dell), replenishment orders from a retailer or distributor (Wal-Mart ordering from P&G), or by the forecast of customer demand and current product availability in the manufacturer’s finished-goods warehouse.
One extreme in a manufacturing cycle is an integrated steel mill that collects orders that are similar enough to enable the manufacturer to produce in large quantities. In this case, the manufacturing cycle is reacting to customer demand (referred to as a pull process). Another extreme is a consumer products firm that must produce in anticipation of demand.
In this case, the manufacturing cycle is anticipating customer demand (referred to as a push process).
The processes involved in the manufacturing cycle include:
- Order arrival from the finished-goods warehouse, distributor, retailer, or customer
- Production scheduling
- Manufacturing and shipping
- Receiving at the distributor, retailer, or customer
1 Order arrival
During this process, a finished-goods warehouse or distributor sets a replenishment order trigger base on the forecast of future demand and current product inventories. The resulting order is then conveyed to the manufacturer.
In other cases, a manufacturer may be producing to stock a finished products warehouse.
2 Production scheduling
This process is similar to the order entry process in the replenishment cycle where inventory is allocated to order. During the production scheduling process, orders (or forecasted orders) are allocated to a production plan.
The objective of the production scheduling process is to maximize the proportion of orders filled on time while keeping costs down.
3 Manufacturing and Scheduling
The objective of the manufacturing and shipping process is to create and ship the product by the promised due date while meeting quality requirements and keeping costs down.
4 Receiving
Procurement cycle
The procurement cycle occurs at the manufacturer/supplier interface. This includes all processes necessary to ensure that materials are available for manufacturing to occur according to schedule.
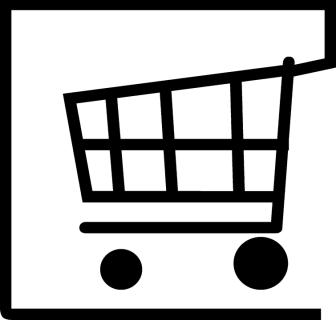
Whereas retailer/distributor orders are triggered by uncertain customer demand, component orders can be determined precisely once the manufacturer has decided what the production schedule will be. Component orders depend on the production schedule.
Thus it is important that suppliers be linked to the manufacturer’s production schedule. Of course, if a supplier’s lead times are long, the supplier has to produce to forecast because the manufacturer’s production schedule may not be fixed that far in advance.
Key point
A cycle view of the supply chain clearly defines the processes involved and the owners of each process. This view is very useful when considering operation decisions.
Because it specifies the roles and responsibilities of each member of the supply chain and the desired outcome for each process.
Reference:
”The 21st Century Retail Supply Chain: The Key Imperatives for Retailers”, Aberdeen Report, 2009